Burners & Combustion Systems
INDUSTRIAL BURNERS AND COMBUSTION SYSTEMS TECHNOLOGY DELIVERING A CLEANER FUTURE
INDUSTRY LEADING LOW NOx PERFORMANCE, PROVEN IN SERVICE
The world’s leading metal producers rely on Bloom Engineering to identify ways to convert their furnaces to hydrogen, decrease CO2, reduce NOX emissions, improve efficiency and melting capabilities, and unlock production capacity in their plants.
Market Applications By Industry
- Reheat Furnaces
- Tunnel Furnaces
- Batch Annealing
- Continuous Galvanizing Lines (CGL)
- Continuous Annealing Lines (CAL)
- Silicon Lines
- Non-Ox Furnaces
- Steckel Mill Furnaces
- Ladle Preheating and Dry-out
- Forge Furnaces
- Soaking Pits
- Hot-Blast Stoves
- Flare Stack Burners and Ignition
- Edge Heaters
- Melting Furnaces
- Round Top
- Rectangular
- Side Well
- Tilting Rotary Furnaces
- Holding Furnaces
- Muffle Furnaces
- Iron Direct Reduction
- Steam Methane Reforming
- Incineration
- Thermal Oxidizers
- Pelletizing
- Sintering Furnaces
- Air Heating & Drying
- LNG Vaporization
Learn more about industrial burner types and options.
Regenerative Burners
A regenerative combustion system uses a pair of burners, each of which has a media case filled with dense ceramic material, which periodically alternate between firing and exhausting. When exhausting, hot combustion products are pulled from the furnace through the burner head and its accompanying media case, increasing the temperature of the ceramic media close to the furnace temperature. When firing, cold air flows through the media case, increasing in temperature to provide oxygen for combustion. After a set period, the burners “cycle” and the previously exhausting burner transitions to firing mode. Regenerative burners capture and return most of the energy contained in the furnace’s waste gases, thereby providing exceptional fuel efficiency for high process temperature applications.
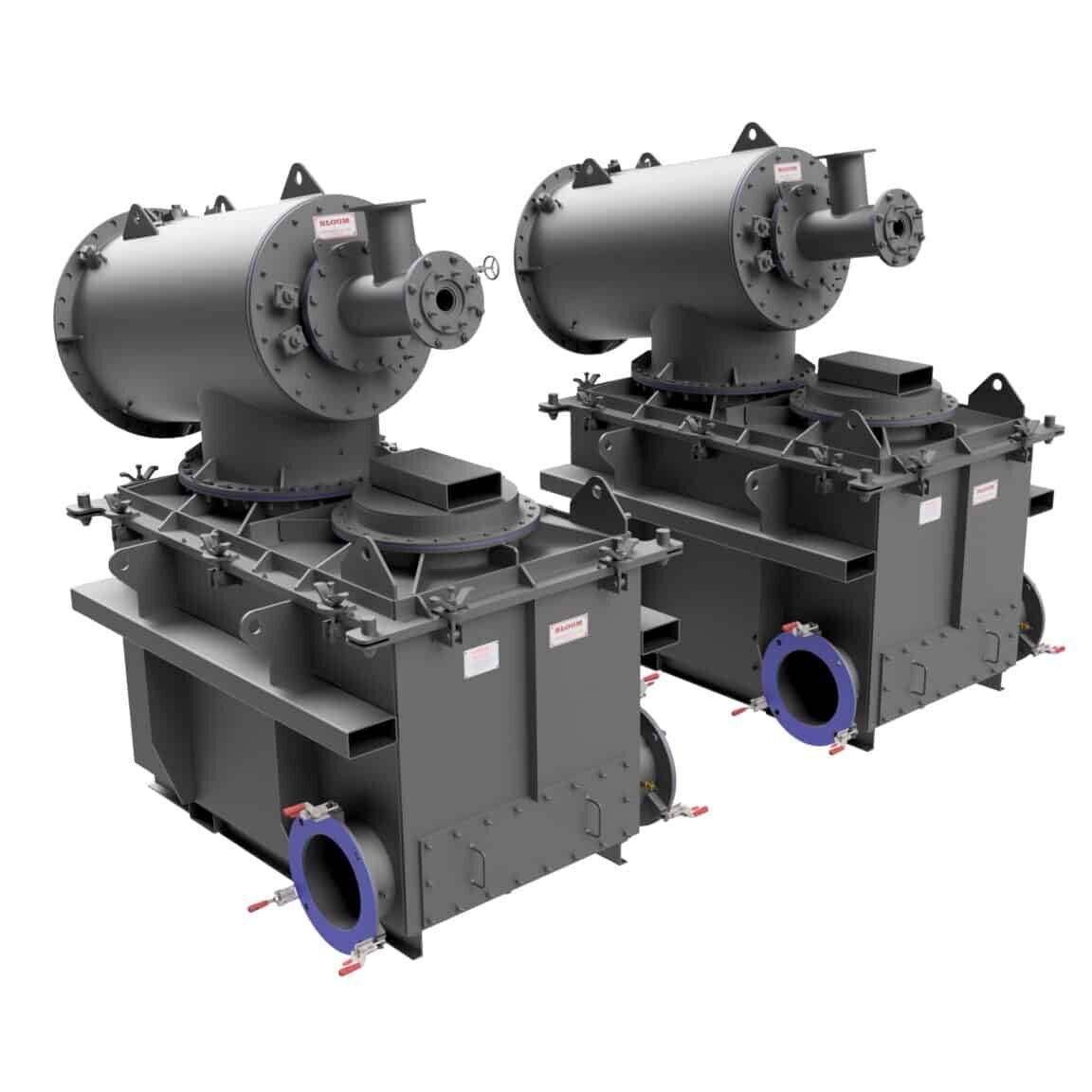
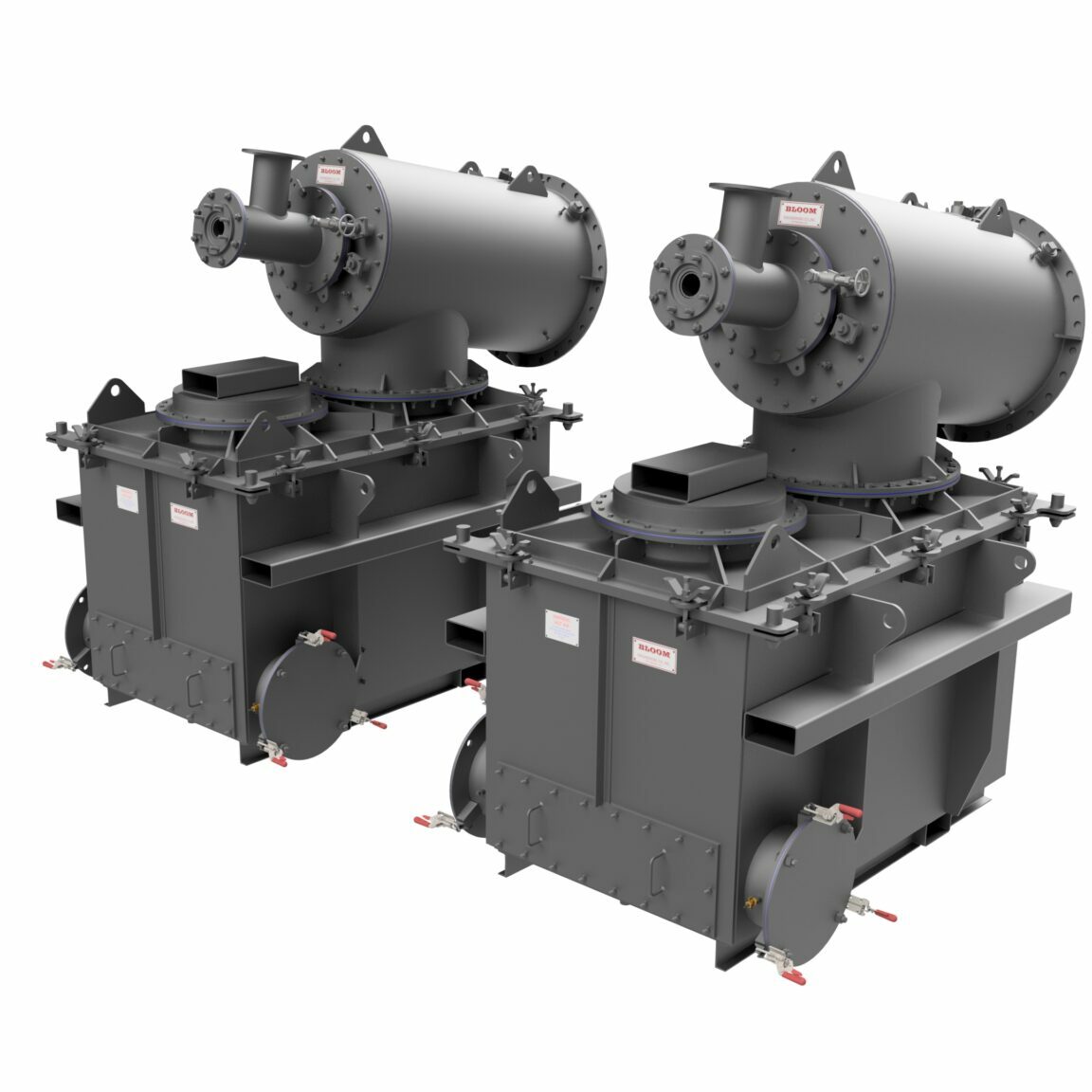
MODELS INCLUDE
- 1100 Series Low NOx
- 1150 Series Ultra Low NOx
- 1650 Regenerative Cyclops™ Ultra Low NOx Burners
- 1160-RG - Ultra Low NOx Lumiflame® Regenerative Burners Optimized for Aluminum Melting furnaces
- 2400-Regenerative HTR®
CAPABILITIES
- World leading low NOx technology
- Reduced carbon dioxide (CO2) emissions
- Can utilize many gaseous and liquid fuels including hydrogen
- Increased production from existing furnaces
- Stable operation from cold start through entire operating range
- Excellent turndown
- Custom engineered for the application
FEATURES
- Refractory baffle protects burner body, stabilizes and shapes the flame, and supports the gas nozzle
- Capacities from 2.5 to 52.5 MMBtu/h - HHV (700 kW to 15,000 kW)
- English and Metric designs
- Flame monitoring using UV detection
- Typical NOx in aluminum melting applications:
- 1150 Series - NOx < 70 ppm @3% O2 (140 Mg/Nm3)
Radiant Tube Burners
Indirect-fired burners where combustion occurs in a radiant tube to prevent contact between the products of combustion and the heating application.
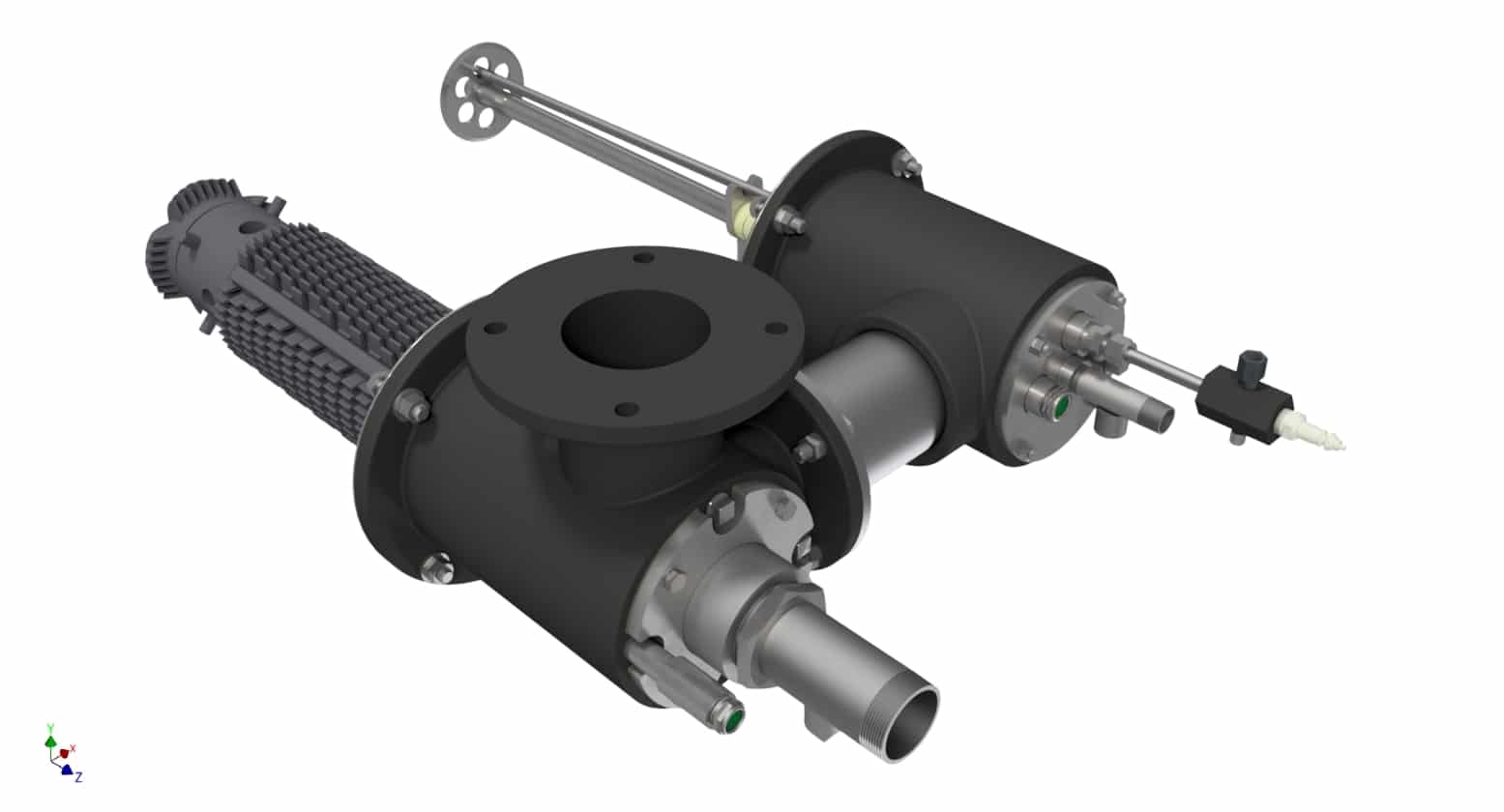
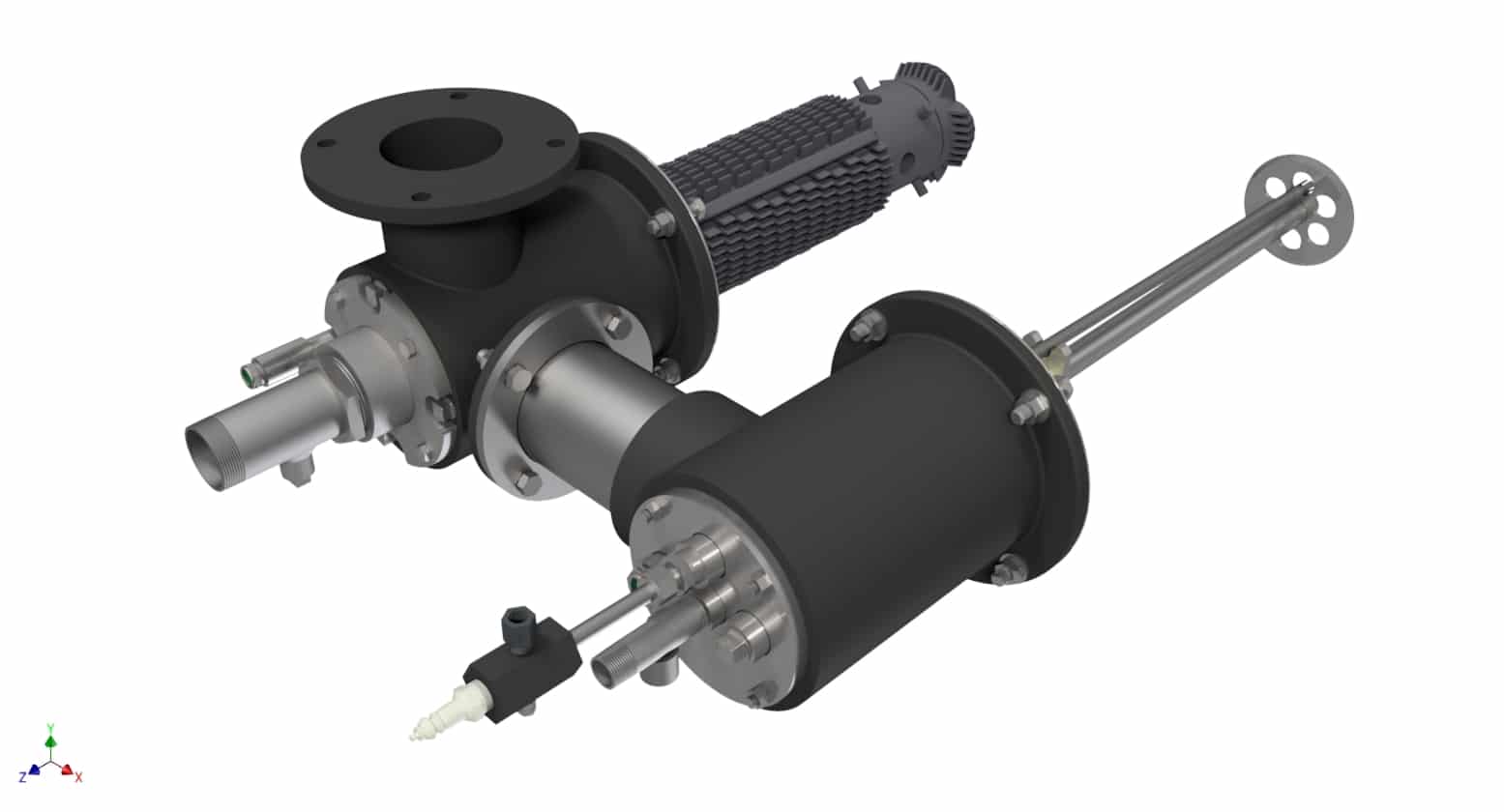
MODELS INCLUDE
- 2301 - Single Ended Radiant Tube Burners
- 2305 - Universal Cold Air Radiant Tube Burners (Pressure Type) – Ultra Low NOx
- 2320 - Recuperative Radiant Tube Burners (Suction Type)
- 2350 - Recuperative Radiant Tube Burners (Forced Air Type)
- 2370 – Recuperative Radiant Tube Burners with Internal Exhaust Gas Recirculation for Ultra Low NOx
- 2460 – Self Recuperative Radiant Tube Burners
CAPABILITIES
- Customizable capacities to suit tube size and heating requirements of the furnace
- Models available with recuperators that can be designed for very high efficiency – as much as 75% (LHV)
- Quite stable operation
- Uniform tube temperature
- Use with cold or recuperated ‘hot’ air
- Compatible with many fuels including
- Natural gas
- Coke Oven Gas (COG)
- Hydrogen
- Propane
- Light Fuel Oil
- Combustion air vitiation for lowest NOx operation
- Options for 4” (100 mm) and larger D. straight, ‘U’, ‘W’, ‘P’, and “Double – P’ tubes
- Designs available for Push, Pull, and Push/Pull systems
- High/Low, On/Off, or Proportional Modulating control
FEATURES
- Rugged construction
- Cast iron burner bodies
- Cast stainless steel recuperator
- Provisions available for flame monitoring
- Designs can be optimized in Bloom’s R&D lab for specific applications
Baffle Burners
Baffle burners consist of a body, gas nozzle, baffle, and port. Baffle burners recirculate furnace exhaust gases into the combustion envelope to limit peak flame temperatures resulting in reduced NOx formation. Baffle burners can run on many types of gaseous and liquid fuels, and they are often designed for multifuel compatibility to increase flexibility for users. Combustion air enters the burner body and is separated from the fuel, which passes through the body inside a fuel tube, until mixing immediately after the baffle. Because fuel and air are not mixed until they exit the hot side of the baffle, flashback is minimized allowing for high turndown and application to fuels with high flame speeds such as hydrogen. The refractory baffle separates and protects the gas nozzle and burner body from the furnace’s thermal radiation, yielding long service life with minimal maintenance.
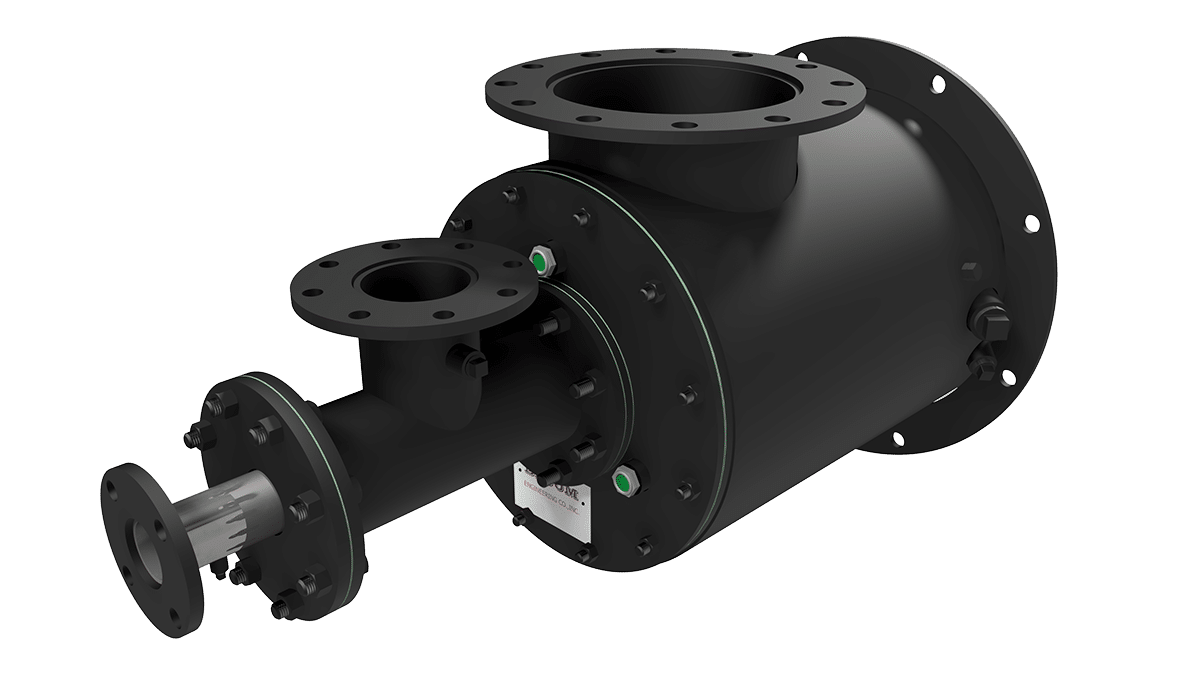
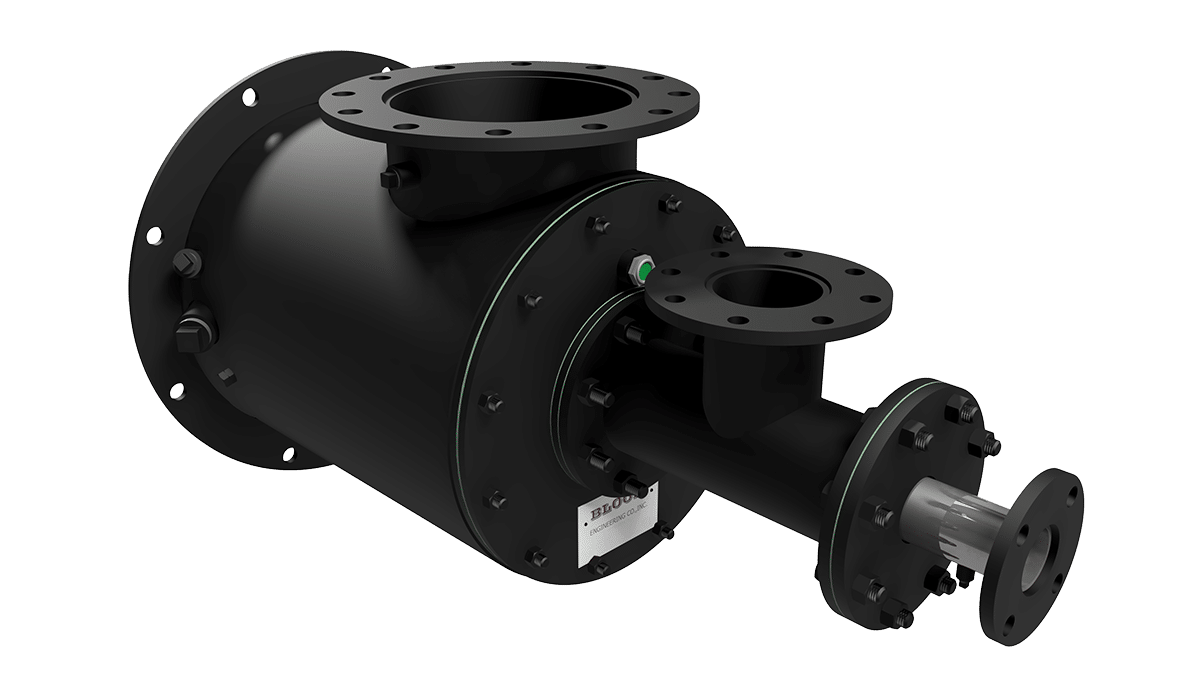
MODELS INCLUDE
- 1020 FTR Cold Air Baffle Burners
- 1200 FTR Hot Air Baffle Burners
- 1030 High Capacity Hot or Cold Air Burners
- 1240-1280 Soaking Pit Burners
- 1360 Uni-Heat® Cold Air Burners with momentum lance
- 1370 Uni-Heat® Hot Air Burners with momentum lance
- 1430 Low NOx Small Capacity Burners
- 1460 Small Capacity Cold Air Medium Velocity Burners
- 1470 Small Capacity Hot Air Medium Velocity Burners
- 1480 Small Capacity Cold Air High Velocity Burners
- 1490 Small Capacity Hot Air High Velocity Burners
- 1600 Large Capacity Hold/Cold Air High Velocity Burners
- Glass Tank Burners (GT)
- High Velocity Burners (HV)
- Minijet Burners (MJ)
CAPABILITIES
- Customizable mounting arrangements
- Quite stable operation
- Stable flames from reducing to highly oxidizing air-to-fuel ratios
- Use with cold or recuperated ‘hot’ air
- Compatible with many fuels including
- Natural gas
- Coke Oven Gas (COG)
- Producer Gas and Blast Furnace Gas (BFG)
- Hydrogen
- Propane and Butane
- Light and Heavy Fuel Oils
- High turndown
- Customizable flame shapes
FEATURES
- Rugged construction
- Cast iron or fabricated steel burner bodies
- Provisions available for flame monitoring
- Capacities from 255,000 Btu/hr to 400+ MMBtu/hr – HHV (75 kW to 117,000 kW)
Air Staged Burners
Air Staged Burners are a Baffle Burner variation that introduce portions of the combustion air at different locations relative to the fuel to delay mixing and decrease peak flame temperatures. Air staged burners tend to have larger flames compared to non-staged and premix burners of the same capacity but produce much lower NOx.
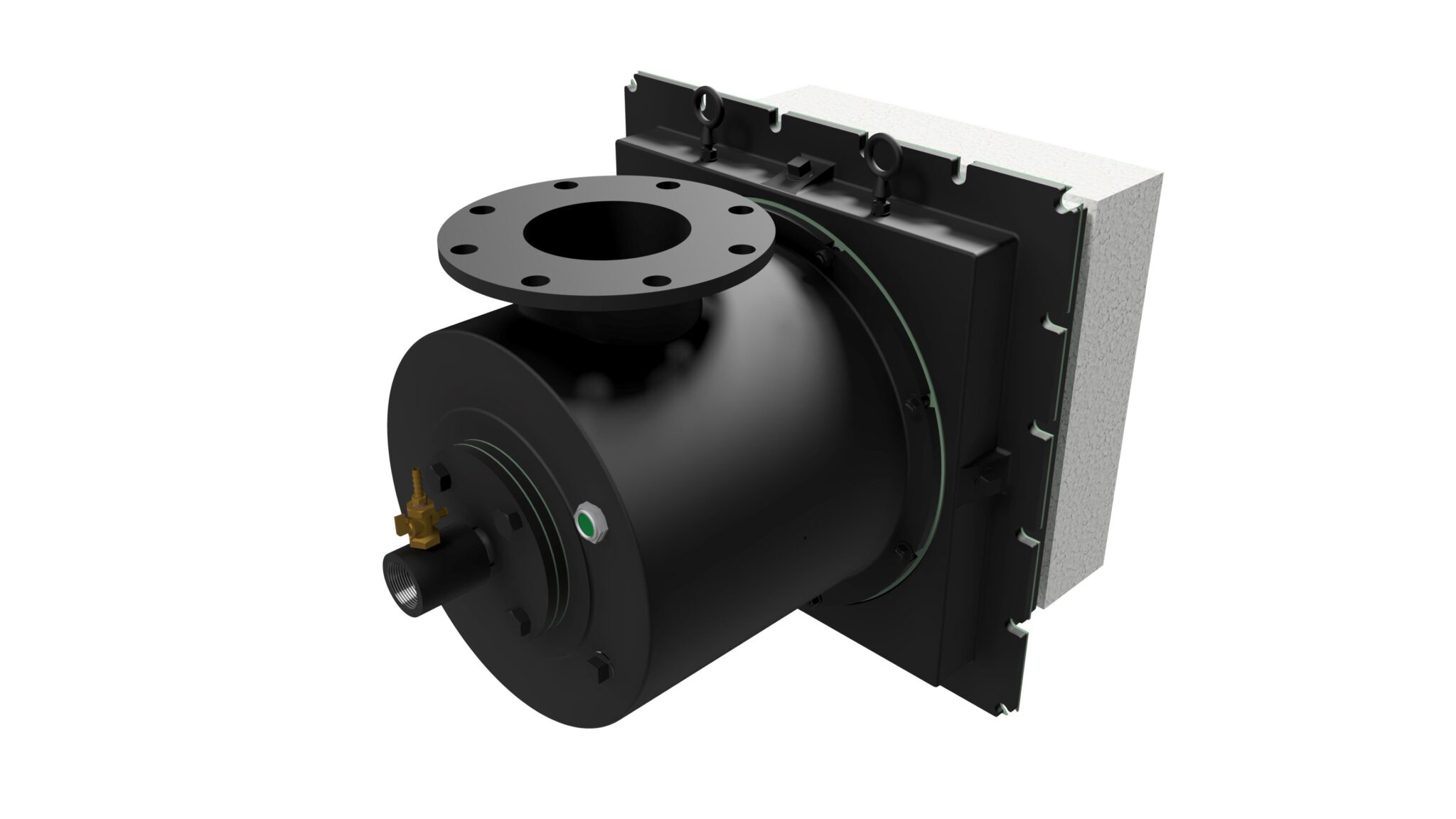
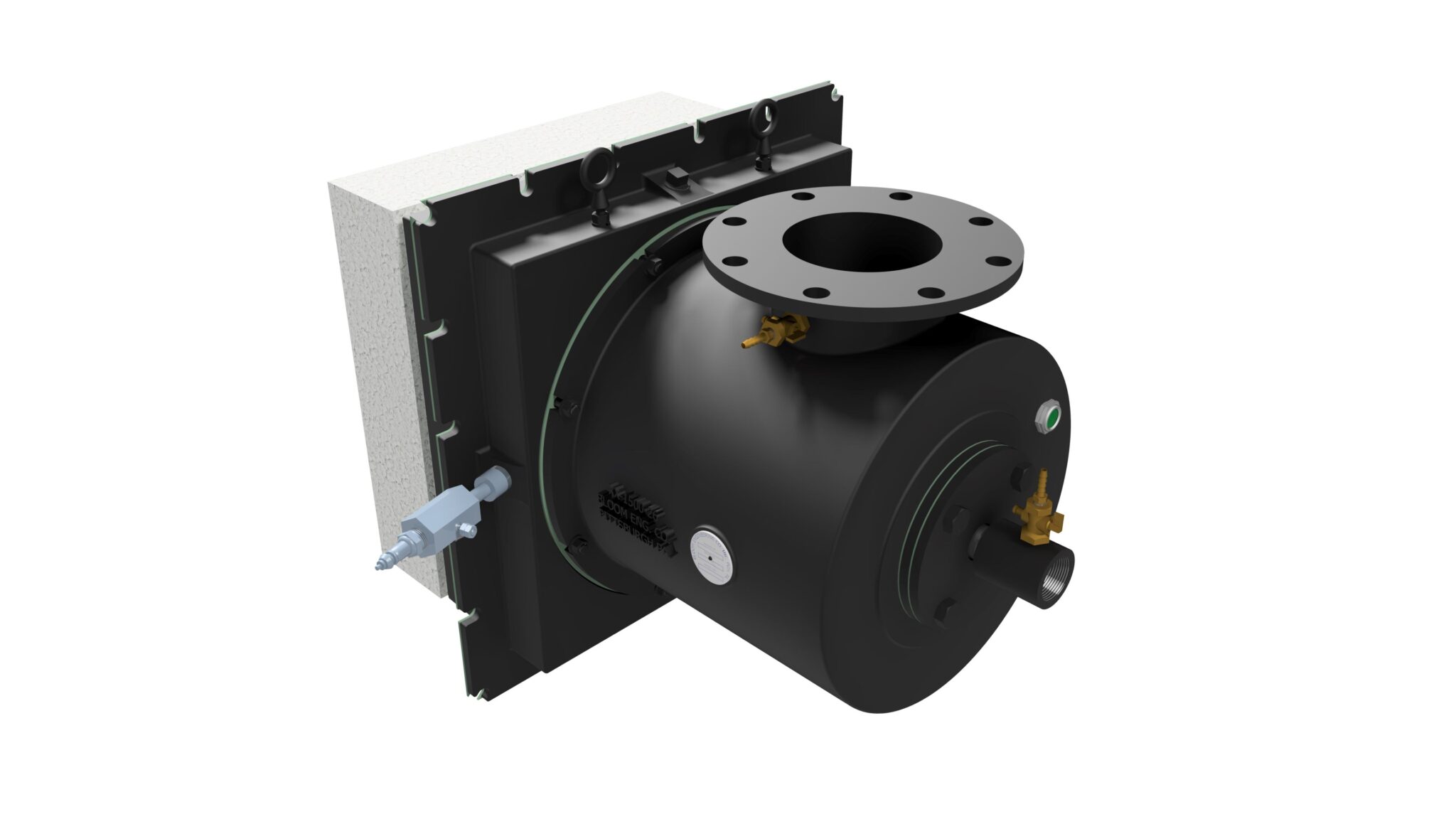
MODELS INCLUDE
- 1500 Series Large Capacity, Ultra Low NOx Burners
- 1500S Series Small Capacity Ultra Low NOx Burners
- 1610 CyclopsTM Series Large Capacity Ultra Low NOx Burners
- 1440 Small and Large Capacity Low NOx Burners
CAPABILITIES
- World leading low NOx technology
- Customizable mounting arrangements
- Quiet operation
- Stable flames from slightly reducing to moderately oxidizing air-to-fuel ratios
- Use with cold or recuperated ‘hot’ air
- Compatible with many fuels including
- Natural gas
- Coke Oven Gas (COG)
- Producer Gas and Blast Furnace Gas (BFG)
- Hydrogen
- Propane and Butane
- Light and Heavy Fuel Oils
- High turndown
- Customizable flame shapes
FEATURES
- Rugged construction
- Cast iron or fabricated steel burner bodies
- Provisions available for flame monitoring
- Capacities from 170,000 Btu/hr to 33.7 MMBtu/hr – HHV (50 kW to 10,000 kW)
Premix and Partial Premix Burners
Premix burners are often used on boilers, air heaters, or ultra-low NOx specialty heat treating applications. Combustion air and fuel are combined before exiting the baffle, differentiating premix from other burner types. One advantage of Bloom premix burners is their very low NOx emissions, especially when operated with moderate levels of excess air. Turndown and fuel compatibility are more limited due to the potential for flashback.
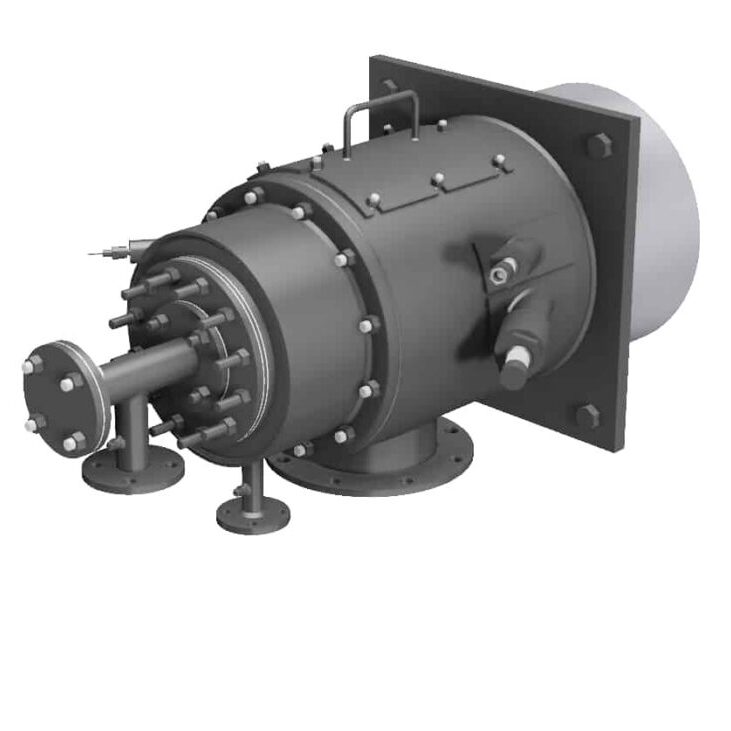
MODELS INCLUDE
- 1230 Ultra Low NOx Cold Air Burners
- 1230S Small Capacity Ultra Low NOx Cold Air Burners
- 1530 Flex NOx Ultra Low NOx Burners
CAPABILITIES
- Ultra Low NOx
- Use with cold air
- Compatible with the following fuels
- Natural Gas (with up to 8% hydrogen enrichment)
- Select clean gaseous fuels
- Light Oil (1530 only)
- Good turndown capability
FEATURES
- Rugged fabricated construction
- Provisions available for flame monitoring
- Capacities from 250,000 Btu/hr to 140+ MMBtu/hr – HHV (73 kW to 41,000 kW)
Self-Recuperative Burners
Self-Recuperative burners incorporate an integral recuperator with the burner which preheats the combustion air. The exhaust gases are ‘pulled back’ through the burner by an eductor or an exhaust ‘suction’ blower. This design allows for increased thermal efficiencies in furnaces where a centralized recuperator is not practical. Bloom Engineering can also pair recuperators with many of its small capacity hot air burners (such as 1500S) for applications where the flame shape or NOx levels of self-recuperative burners are not optimal.
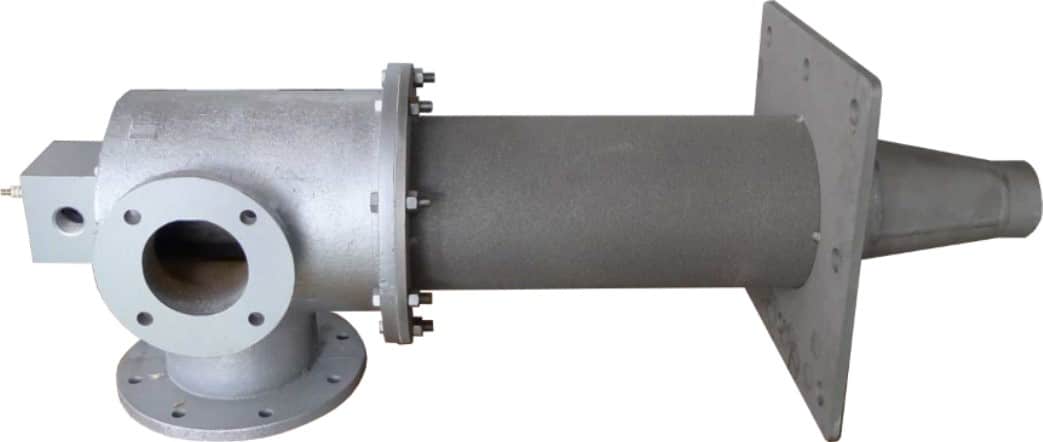
MODELS INCLUDE
- 2450 Series, Self-Recuperative Burners
- Heat Recovery Burners (HRB)
CAPABILITIES
- Use with cold air
- Models available for use with the following fuels
- Natural Gas
- LPG
- Manufactured Gas
- Light Oil
- Good turndown capability
- Options available for furnace temperatures up to 2,282°F (1250°C)
FEATURES
- Rugged fabricated construction
- Provisions available for flame monitoring
- Capacities from 213,000 Btu/hr to 2.75 MMBtu/hr – HHV (62 kW to 800 kW)
High Thermal Release (HTR®) Burners
High Thermal Release (HTR®) Burners are similar to baffle burners and produce a flame shape that lies flat against a furnace’s wall or roof, providing maximum radiative heat transfer without the risk of flame impingement.
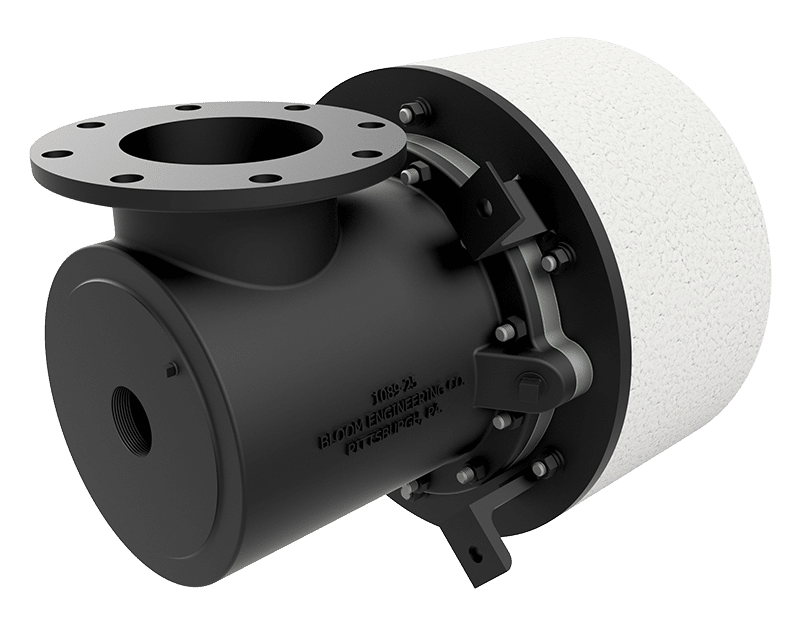
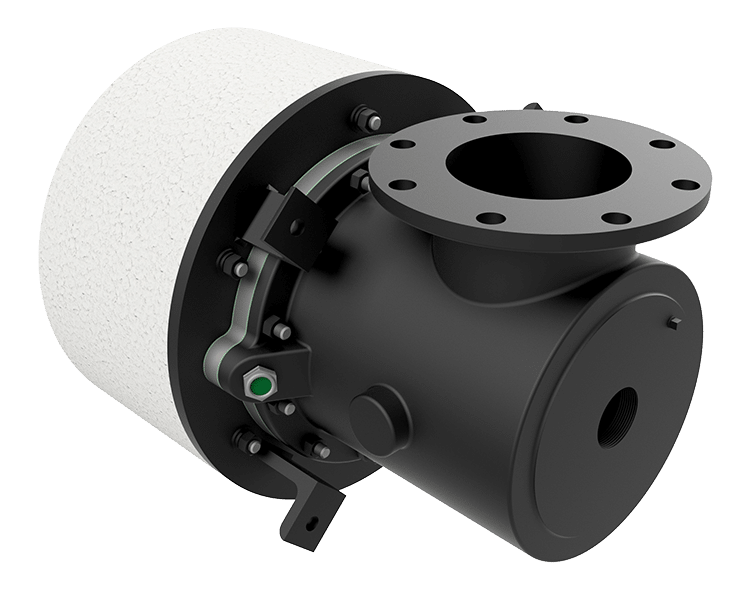
MODELS INCLUDE
- 2000 Series Cold Air (HTR®) Burners
- 2100 Series Hot Air (HTR®) Burners
- 2180 Series Air Staged Ultra Low NOx (HTR®) Burners
- 2190 Series Gas Staged Ultra Low NOx (HTR®) Burners
CAPABILITIES
- World leading low NOx technology
- High thermal turndown
- Models offered that are compatible with many fuels including
- Natural gas
- Coke Oven Gas (COG)
- Hydrogen
- Propane
- Fuel Oil
- Mixed Gases
FEATURES
- Capacities from <70,000 to > 4.4 MMBtuh - HHV (12 kW to 1,300 kW)
- Wall mounted or roof mounted versions available
- Square or round port blocks
Combustion Controls Systems
Bloom Engineering provides complete combustion control solutions from concept through design-build, commissioning, training and follow up support. A wide variety of standard and custom-designed combustion controls systems can be furnished to meet customer requirements.
Current and future demands for high efficiency, low emissions and maximum furnace productivity require a well-engineered control system, with detailed application knowledge of the furnace operation and interaction with the burner system.
Bloom Engineering conducts complete functional testing of hardware and software, greatly reducing field commissioning time and enhancing long term reliability. Our design philosophy considers harsh environmental factors such as temperature, dust, vibration, and electrical noise.
With safety and reliability as a primary system design consideration, combustion control packages are available to meet industry-accepted codes and standards including:
- NFPA 85 (boilers)
- NFPA 86 (furnaces)
- NFPA 87 (fluid heaters)
- EN 746-2
- CSA B149.3/TSSA
- And Hazardous Locations as defined by NEC, ATEX, and KOSHA
Ladle and Tundish Heating, Edge Heaters, and Drying Stations
A complete line of packaged heating and drying stations for horizontal and vertical applications are available. Testing prior to shipment ensures minimum commissioning time. Each unit is custom engineered to the application’s needs. To meet specific requirements for CO2 or fuel cost reduction, Bloom Engineering offers high efficiency designs that utilize preheated combustion air. For maximum efficiency, regenerative systems or oxygen-enriched burners are also an option. Where simplicity of operation, ease of maintenance, and minimizing project cost are primary considerations, conventional cold air baffle burners or premix burners offer excellent solutions.
Low Temperature Regenerative (LTRTM ) Combustion System
The Low Temperature Regenerative (LTR TM) heat recovery system was developed for continuous or batch furnaces with a variety of burner configurations, control zones, and operating temperatures up to approximately 1600°F (870°C), where maximum heat transfer and burner efficiency is required. LTR TM systems rely on ceramic media for heat recovery from exhaust gases and offer a highly efficient alternative to metallic recuperators.
Customized solutions to meet your needs.
Bloom Engineering’s product line is not just limited to the products you see listed. We can help guide and develop a customized system that addresses your unique requirements. Connect with a Bloom Engineering Specialist Today.